Sewage Sludge Disc Dryer
Advantages:
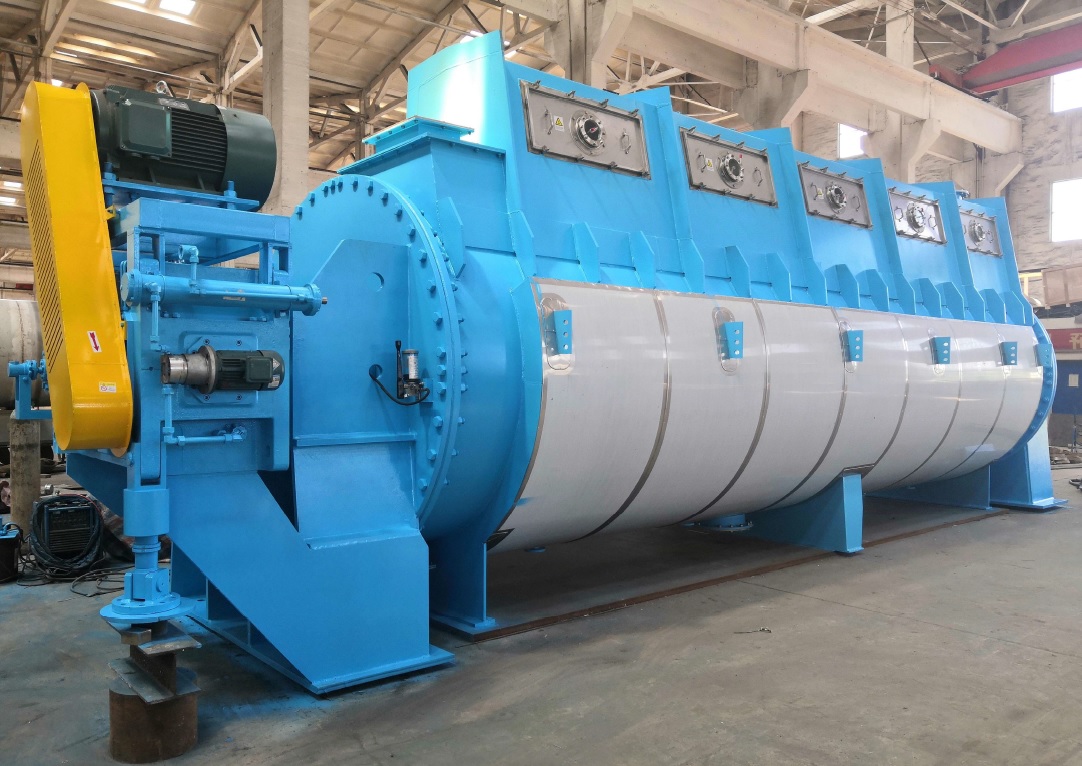
How does a sewage sludge disc dryer work - working principle
Drying of sewage sludge is performed by using saturated steam in the pressure range of 6 to 10 barG and temperatures from 158 °C - 180 °C. It consists of a rotor and a stator. Double-wall discs are welded perpendicularly to the rotor. Heat is transferred indirectly from steam to the dried material by the heating process. Extra capacity can be achieved by adding to the stator heated steam jacket. The dried product is continuously moved and mixed by the paddles along the machine. Scrapers welded to a stator ensure continuous mixing and are preventing material from sticking to the discs. The dried material is unloaded by a screw conveyor mounted at the end of the dryer. Contaminated vapor flies out by a centrally placed vapor dome to the exhaust gases treatment system.
Drying technology have been invented in the 1960s and was designed and developed for fish meal. Disc dryer is still used for sludge incineration plants for partial and full drying. Over the years, it has turned out that the life of the dryers can reach almost 30 years. Productivity ranges from 1000 kg/h to 5000 kg/h depending on the size of the machine.
Characteristics of a sludge disc dryer for partial drying
Disc dryer is designed for partial drying of dewatered sludge. Thanks to high water vaporization, it is perfect for capacity expansion of the existing plants and for sewage sludge mono-incineration installations. The dryer is very accurate, it is possible to achieve the required drying rate (DR). Thermal drying is necessary to remove the water that cannot be separated mechanically. The machine is made to handle sticky materials. Specially designed rotary dryer for materials with high humidity, viscosity, and low heat value, such as sludge. The compact design of the machine guarantees the high efficiency of water vapor evaporation. The rotor can be made from stainless or carbon steel. The stator is delivered mostly in stainless steel. If sludge contains sand or crystal magnesium-ammonium-phosphate, then the drying machine is made from better quality stainless steel, is more resistant to wear and tear. Dryer capacity is depending on water content and heat transfer of dried material. Machines are available in different sizes. The required operating capacity of the dryer can be achieved by changing the size of the dryer. Sludge dewatering machine is widely used in municipal wastewater treatment plants.
Sludge drying process
Sludge is delivered from the raw material bin to the dryer inlet, which is placed on the top of the stator. Transportation of sludge can be done by a pump or screw conveyor. The speed of the machine can be changed by the frequency converter mounted at the gear motor. Saturated steam is released from the steam boiler to the rotor and to the discs. The heating process of sludge is started and mixing takes place by the paddles which are welded to the discs. The surface area of the sludge dryer affects effectively the vaporization process of water vapor. Before thermal processing, dewatered sludge have a drying rate between 20 - 30%. After the drying rate is changed to 40-45%. Dried sludge leaves the dryer together with contaminated vapor, which flies out by the vapor dome. The waste heat of the vapor can be utilized for heating some other network or machine. Treatment of the contaminated vapor condensate is necessary because it contains solids, ammonium, and dissolved COD.
If you need more information about the available solutions, please contact us via the contact form on the last tab, by e-mail: info@tg-machines.com or call us.
For more technical information, please download our technical data sheet.